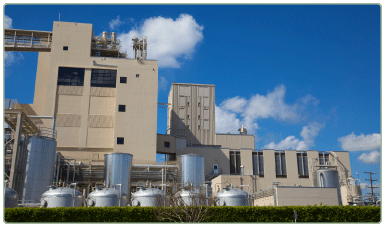
COIR EZ Seed
The COIR EZ Seed project consisted of the design, construction, start-up and commissioning of a manufacturing (process, blending, packaging) and warehouse facility. The process area (Class II, Division II) included raw material (COIR) handling, shredding, transfer, aspiration, milling (size reduction), volumetric feeders, compaction, milling and screening loop, material handling (pneumatic transfer) and bulk bag filling and storage. The blending process consisted of pneumatic transfer, bulk bag unloading and pneumatic transfer, weigh belt and vibratory feeders, blending, belt conveyor and storage.
Subhead Title
The process and blending electrical load was in excess of 3,600 HP. The packaging process included 10 and 20/40 lb bag filling (volumetric and gravimetric), check weigher, bag sealer, labeling, case forming and sealing, robotic case packing, robotic palletizing and stretch wrapping. In addition, the packaging process included a jug filler, with bottle depalletizer, jug orienter, labeler, capper, case forming and sealing, robotic case packing, robotic palletizing and stretch wrapping. Ventura was responsible for the design, specification and selection of the equipment listed above.
Subhead Title
Engineering services consisted of detailed design and bid package preparation including, demolition, architectural, civil, structural, process, mechanical, HVAC, communications (copper and wireless Ethernet) and electrical (Power and Controls). Ventura provided the PLC programming and developed the HMI screens as part of this project. In addition, Ventura provided construction management, equipment check-out, I/O checkout, commissioning, start-up and troubleshooting support for all process systems.
Subhead Title
This project included a demolition package, site work, major modification to the site storm water drainage, dock relocation, 37,000 S.F. warehouse addition, new trailer drop area, new truck entrance and exit, new raw material dock area, 15’ height increase to an existing process tower, all structural building modifications, equipment general arrangement drawings (process, blending, packaging), equipment millwright package (process, blending, packaging), new substation, New MCC’s, 480V and 120V power to equipment, instrumentation and controls package, dust collection duct design, process duct design, mechanical (compressed air, natural gas, water, binder piping, building HVAC, control room and MCC HVAC, air permit preparation, building permit applications, and process hazard analysis.
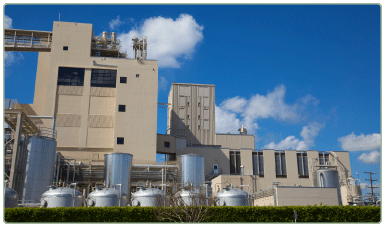
Project Two
The COIR EZ Seed project consisted of the design, construction, start-up and commissioning of a manufacturing (process, blending, packaging) and warehouse facility. The process area (Class II, Division II) included raw material (COIR) handling, shredding, transfer, aspiration, milling (size reduction), volumetric feeders, compaction, milling and screening loop, material handling (pneumatic transfer) and bulk bag filling and storage. The blending process consisted of pneumatic transfer, bulk bag unloading and pneumatic transfer, weigh belt and vibratory feeders, blending, belt conveyor and storage.
Subhead Title
The process and blending electrical load was in excess of 3,600 HP. The packaging process included 10 and 20/40 lb bag filling (volumetric and gravimetric), check weigher, bag sealer, labeling, case forming and sealing, robotic case packing, robotic palletizing and stretch wrapping. In addition, the packaging process included a jug filler, with bottle depalletizer, jug orienter, labeler, capper, case forming and sealing, robotic case packing, robotic palletizing and stretch wrapping. Ventura was responsible for the design, specification and selection of the equipment listed above.
Subhead Title
Engineering services consisted of detailed design and bid package preparation including, demolition, architectural, civil, structural, process, mechanical, HVAC, communications (copper and wireless Ethernet) and electrical (Power and Controls). Ventura provided the PLC programming and developed the HMI screens as part of this project. In addition, Ventura provided construction management, equipment check-out, I/O checkout, commissioning, start-up and troubleshooting support for all process systems.
Subhead Title
This project included a demolition package, site work, major modification to the site storm water drainage, dock relocation, 37,000 S.F. warehouse addition, new trailer drop area, new truck entrance and exit, new raw material dock area, 15’ height increase to an existing process tower, all structural building modifications, equipment general arrangement drawings (process, blending, packaging), equipment millwright package (process, blending, packaging), new substation, New MCC’s, 480V and 120V power to equipment, instrumentation and controls package, dust collection duct design, process duct design, mechanical (compressed air, natural gas, water, binder piping, building HVAC, control room and MCC HVAC, air permit preparation, building permit applications, and process hazard analysis.
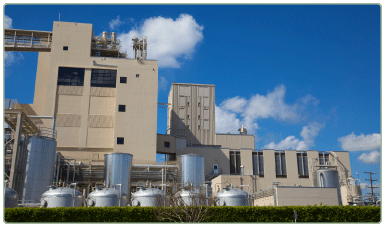
Project Three
The COIR EZ Seed project consisted of the design, construction, start-up and commissioning of a manufacturing (process, blending, packaging) and warehouse facility. The process area (Class II, Division II) included raw material (COIR) handling, shredding, transfer, aspiration, milling (size reduction), volumetric feeders, compaction, milling and screening loop, material handling (pneumatic transfer) and bulk bag filling and storage. The blending process consisted of pneumatic transfer, bulk bag unloading and pneumatic transfer, weigh belt and vibratory feeders, blending, belt conveyor and storage.
Subhead Title
The process and blending electrical load was in excess of 3,600 HP. The packaging process included 10 and 20/40 lb bag filling (volumetric and gravimetric), check weigher, bag sealer, labeling, case forming and sealing, robotic case packing, robotic palletizing and stretch wrapping. In addition, the packaging process included a jug filler, with bottle depalletizer, jug orienter, labeler, capper, case forming and sealing, robotic case packing, robotic palletizing and stretch wrapping. Ventura was responsible for the design, specification and selection of the equipment listed above.
Subhead Title
Engineering services consisted of detailed design and bid package preparation including, demolition, architectural, civil, structural, process, mechanical, HVAC, communications (copper and wireless Ethernet) and electrical (Power and Controls). Ventura provided the PLC programming and developed the HMI screens as part of this project. In addition, Ventura provided construction management, equipment check-out, I/O checkout, commissioning, start-up and troubleshooting support for all process systems.
Subhead Title
This project included a demolition package, site work, major modification to the site storm water drainage, dock relocation, 37,000 S.F. warehouse addition, new trailer drop area, new truck entrance and exit, new raw material dock area, 15’ height increase to an existing process tower, all structural building modifications, equipment general arrangement drawings (process, blending, packaging), equipment millwright package (process, blending, packaging), new substation, New MCC’s, 480V and 120V power to equipment, instrumentation and controls package, dust collection duct design, process duct design, mechanical (compressed air, natural gas, water, binder piping, building HVAC, control room and MCC HVAC, air permit preparation, building permit applications, and process hazard analysis.